Inventory Accuracy
- Michael Roberts, CEO, Physec Compliance Group LLC
- Jul 4, 2016
- 6 min read
Given the option of getting a voluntary root canal instead of physically counting inventory, many of us would likely being calling our dentist right now. Certainly, physical inventory can be a painful process, especially for retail businesses doing their best just to get orders out to the customer. However, accurate inventory can help reduce a long list of problems with which many of us are familiar:
Wasting time looking for items
Holding extra inventory as a safety stock against inaccurate numbers
Avoiding orders for older items because we’re not sure that we still have what our system says we do …. And we all know about this.
Expediting reorders because we suddenly can’t find any more of the product
Below are ten tips that will make physical inventory counting much smoother, so we as a team can continue providing the best possible customer service in the company.
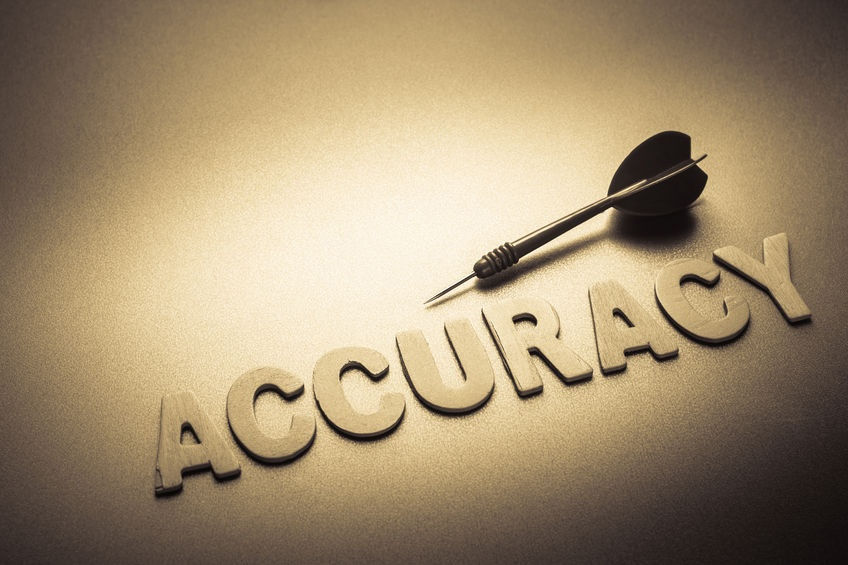
1 – Make Inventory Accuracy a Higher Priority than Order Fulfillment
Raising the priority of accurate inventory is perhaps the most important, yet most difficult, step in inventory accuracy. Many inventory problems arise from pushing a transaction through the system with the intent of going back and fixing the numbers later. As most of us are well aware of. In the rush of other emergencies, however, we often forget to go back and correct the numbers in the system. This leads from and to missed production entries, negative lines of inventory, and a whole mess of other problems. Only by putting systems in place that will prevent an employee from moving forward without the necessary system transaction can you effectively keep accurate records of inventory.
One example of a successful implementation that I have seen was changing the accounting system so that it will not process any shipment that contains more inventory than they have on hand. For example, if they’re trying to ship 15 of an item, but their system says they only have 5 in stock, then an alert will pop up and force them to fix the problem before moving forward. This helps them address problems before the product goes out the door. By forcing them to address missed production entries before the product leaves, their modified system helped them eliminate most of their major inventory issues.
2 – Put Everything in a Marked Location
When the time comes to count inventory, having everything in a marked location is a necessity. Those loose boxes and stray pallets without a home are often the problems that come back to haunt us while we try to reconcile. Even if we must make new, temporary locations for the duration of the count, put everything in a well-marked and defined place, and leave it there.
3 – Reduce Inventory as Much as Possible
Do all we can to count as little inventory as possible. Whether it’s holding up an inbound shipment a couple days, or shipping extra in the days prior to the count, counting less means fewer chances for mistakes. We will also want to be sure to not receive or ship any product during the count, since this can easily cause discrepancies.
4 – Count Overstock Locations Beforehand
Even before the count has started, counting the overstock locations beforehand can mean much less counting on the days that inventory is frozen. Fully stocking the picking locations first, then wrapping and marking the count of overstock location can drastically reduce the stress on count day. However, be sure that if inventory is taken from the overstock location, the count tag is either removed or adjusted to the lower quantity.
5 – Be Visual with Counts
With so many people counting, keeping track of what has and has not been counted can often be difficult. To avoid confusion, be extra generous with visual labels and controls. Large count tags, bright colors, and unmistakably clear signs can save you hours of confusion later on. Especially if you are bringing in employees or temps unfamiliar with your product, erring on the side of too big and obvious can be well worth the expense. If something is not in inventory, mark it so even those with the poorest of eyesight can easily understand to not count the product.
6 – Have Someone Familiar with the Product on Every Count Team
Another problem that I have encountered is the unit of measure of items to count. Is an assortment of 24 items in inventory as 1 pack or 24 eaches? While box markings can help, nothing replaces an experienced team member. If you bring in additional people to help count, be sure to include someone who knows the products well on each team. Partnerships with one experienced person and one new work well.
7 – Be Quick and Creative with Immaterial Counts
Some small items aren’t worth the effort to count individually. Whether its tiny plastic bags, plastic hooks, tons of grain, or gallons of chemicals, physically counting out the amount is often not worth the value of the product. For large quantities of small items, a sensitive scale is the best method. Weighing out a sample and then calculating piece count from the total weight is accurate enough for an inexpensive component. For large quantities that are difficult to weigh, calculating volume by lead lines and extrapolating is preferable to simply guessing.
8 – Audit Counts Right After the Count Starts
Auditing counts are essential to ensure each team is counting the products correctly. However, if we wait until all the counting is done, we can’t do much but go back and recount whatever that team counted. Instead, auditing counts from each team soon after they start gives us an opportunity to correct any problems and train more to avoid future miscounts.
9 – Discipline Ourselves to Regular Cycle Counts
As our to-do list grows, taking time to cycle count is likely to slip to the very bottom of your priorities. However, installing incentives and consequences to ensure regular cycle counts happen will not only reduce the pain of a complete physical count, but also give us more confidence in our system’s numbers throughout the year. Whether we schedule our cycle counts based on ABC analysis (see below), items likely to have problems, or some other method suited to our business, rotating through items helps catch inventory issues before they become larger problems.
10 – Review Problems and Change
Finally, One of the most critical stages.....is after we’ve recorded our last counts and everything is reconciled in our system, take a few minutes to reflect. Gather the team together and review what problems we encountered. What went well? What caused problems? Most importantly, what can we put in place to avoid these same problems in the future? Each small change that we put in place today can save our team headaches in the future.
ABC analysis
ABC analysis divides an inventory into three categories- "A items" with very tight control and accurate records, "B items" with less tightly controlled and good records, and "C items" with the simplest controls possible and minimal records.
The ABC analysis provides a mechanism for identifying items that will have a significant impact on overall inventory cost, while also providing a mechanism for identifying different categories of stock that will require different management and controls.
The ABC analysis suggests that inventories of an organization are not of equal value. Thus, the inventory is grouped into three categories (A, B, and C) in order of their estimated importance.
'A' items are very important for an organization. Because of the high value of these 'A' items, frequent value analysis is required. In addition to that, an organization needs to choose an appropriate order pattern (e.g. ‘Just- in- time’) to avoid excess capacity. 'B' items are important, but of course less important than 'A' items and more important than 'C' items. Therefore 'B' items are intergroup items. 'C' items are marginally important.
ABC analysis categories
There are no fixed threshold for each class, different proportion can be applied based on objective and criteria. ABC Analysis is similar to the Pareto principle in that the 'A' items will typically account for a large proportion of the overall value but a small percentage of number of items. Example of ABC class are
‘A’ items – 20% of the items accounts for 70% of the annual consumption value of the items.
‘B’ items - 30% of the items accounts for 25% of the annual consumption value of the items.
‘C’ items - 50% of the items accounts for 5% of the annual consumption value of the items.
Another recommended breakdown of ABC classes:[4]
"A" approximately 10% of items or 66.6% of value
"B" approximately 20% of items or 23.3% of value
"C" approximately 70% of items or 10.1% of value
Comments