Improve your Safety Management Mindset
- Michael Roberts, CEO, Physec Compliance Group LLC
- Jun 20, 2016
- 3 min read
Achieving sustainable improvements in safety performance often requires a change in the way an organization approaches and thinks about safety. . . a paradigm shift.
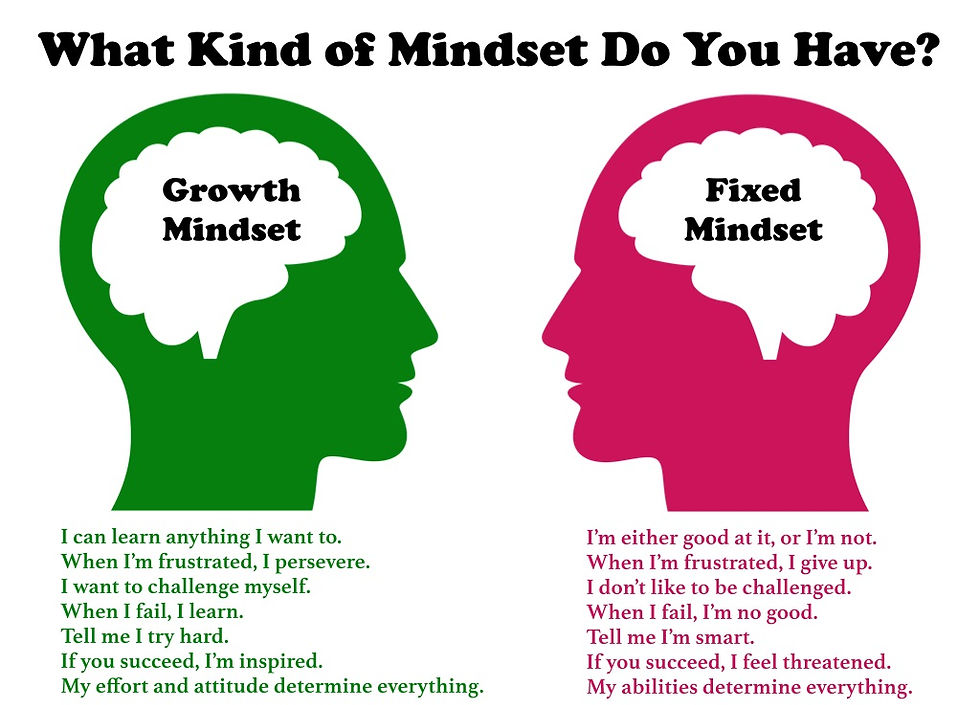
While moving from a comfort zone can be intimidating, considering three important building blocks can help you make the shift successfully:
Perception, system and values.
1. PERCEPTION: RESPONSIBILITY, TEAMWORK AND OWNERSHIP
Safety performance requirements are all too often viewed as a necessary evil driven by the risk of liability under regulatory standards from agencies such as OSHA and DOT. These requirements should be viewed as organizationally (and individually) directed responsibilities that benefit all parties.
Perceptions are important because working to achieve one’s own safety goals is much more motivating than attempting to satisfy the requirements established by some outside regulatory agency. In addition, when employees function as a team to achieve targeted results and self-imposed objectives the working environment is far more positive than it is when individuals see their efforts as an attempt to avoid negative consequences, such as fines, penalties, injuries and safety-related incidents.
As organizations move from a failure-avoidance to an achievement-oriented mindset, employees will have greater involvement in the safety management process and a greater sense of ownership in it. Management’s role in this shift is to provide visible support, facilitate the process, empower the workforce and lead by example, versus attempting to drive or control the process and set requirements from the top.
2. THE SAFETY SYSTEM PROCESS
To succeed, a safety management improvement process must address all three fundamental elements of the safety management triangle:
Work Environment:This includes equipment, housekeeping and engineered systems;
People:The knowledge, skills, abilities, values and attitudes of the people in the workplace; and
Behaviors:This encompasses the performance of assignments, observations, communications, etc.
Safety programs are a key component of the process. Programs add significant value by providing for targeted activities that are designed to support and refresh the process and its objectives.
However, safety programs should not be viewed as the process in its entirety. If the system and the process become ends in themselves, employees and line managers lose sight of the vision and long term mission and what you end up with is a piecemeal approach to safety results, the weakening of commitment and, ultimately, the thwarting of progress.
Accountability is the most critical aspect of the safety improvement process. An accountability system needs to be in place for employees and all levels of line management. The role of the system is to define roles and responsibilities, goals and objectives, targeted activities, measurements for progress and success, reporting mechanisms, assessment methods and consequences for results (both positive and negative).
Effective management of the safety improvement process cannot occur without measurement. Methods can and should be developed to gauge organizational progress for each of the process elements. Goals and objectives, both activity-based and results-oriented, need to be objectively assessed. Line management must be held accountable for the achievement of goals. And, most importantly, success should be recognized and celebrated.
3. VALUE VS. PRIORITY
We hear organizations state that “safety is our #1 priority.” But what does that really mean? Of course, all companies want their workers to be safe and healthy. But priorities shift as urgencies change. What doesn’t shift in the face of changing circumstances are values, that is, a group or individual’s accepted principles and standards.
Though, to sustain improvements and achieve lasting results, the organization must make safety not just a priority but a core value. Turning safety into a core value is not easy. Literally hundreds of books have been written on this subject and it’s clearly beyond the scope of my article to offer a solution. Still, what I can do is give you as safety professionals a sense of the stakes involved in championing the effort to make your organizations embrace safety as a value.
CONCLUSION
As in most endeavors, patience is a virtue in safety management. There are no quick fixes. The essence of success in safety is continuous improvement. This does not mean 100% progress or the absence of setbacks along the way. Continuous progress is often a lot like the teaching a baby to walk: two steps forward and one step back. Happening or developing gradually or in stages; proceeding step by step.. Eventually, we realize that we can let go of the hands and the baby walks all by itself. The movement or development toward a destination or progression to a more advanced state, gradually or in stages.
If you want to make those two steps forward, you’ll need to display the “3 C’s” of organizational or cultural change:
Champions to lead and manage the change process;
Commitment to and a sense of ownership in the process; and
Consistency in actions and words.
Comments