Complacency, the silent killer.
- Michael Roberts, CEO, Physec Compliance Group LLC
- Jun 11, 2016
- 6 min read

There seems to be an upward trend in several industries to list "complacency" as a contributory cause on accident investigation reports. Many perception surveys now ask workers if they have become complacent when doing repetitious jobs and if complacency is considered an undesirable characteristic of a safety culture. Although this attention to complacency is deserved, the standard solutions to improve it fall short of success in almost all instances. Complacency is a state of mind, which is not necessarily the only influence on safety choices or behaviors.
Job site safety is an ever-present issue that is a constant threat in any environment and in any walk of life. The greatest way to prevent accidents is to train people how to reduce the risk to zero or how to put controls in place that will limit the possibility of an accident. Workplace mishaps can be dramatically reduced with the correct mindset and attitude by recognizing four common errors that open the door to injury:
1) Rushing Employees often feel constant pressure to complete tasks as quickly as possible so that they can move onto the next task or finish the day early. Rushing reduces the quality of workmanship and increases the chances of not following the correct safety steps to complete tasks. Accidents increase on Fridays, holiday weekends or when jobs are behind schedule. It’s important to remind employees that working safety is the first priority, even if it means finishing the job later. 2) Frustration Frustration is a mindset that almost everybody experiences at some point in life. Having the right tools to manage frustration and turn negatives into positives is key to being able to avoid accidents and injuries. Creating a workplace that prevents frustration from developing is key. Employees can get frustrated at poor procedures, bad communication, wrong or insufficient materials and problems at home. Not all situations can be managed and controlled, but hiring employees that can control their emotions is a valuable practice to any company. 3) Fatigue Fatigue greatly reduces production and performance. A tired driver is said to be as dangerous on the road as a drunk driver, which illustrates the dangers of fatigue. It is very important to identify when a worker is fatigued to take the correct cause of action. A great danger in hotter climates is heat stress, which causes fatigue and can result in death. Having heat stress safety plans are an essential training topic for all work forces. To avoid fatigue, employees should not overwork or work overly long hours. Corporations have to set realistic deadlines and attainable goals for employees. 4) Complacency Complacency can be the most dangerous mindset that results in an injury or accident. The first step to an accident involves the false belief that experience makes you invulnerable. Accidents can happen to anybody at any time and one’s sense should always be finely tuned to each situation’s risks. A false sense of security is the result of poor training and following bad practices, which leads to accidents.
Management needs to be quick to intervene when boredom results in complacency. These mindsets can cause or contribute to critical errors which increase the probability of injury:
Eyes not on task
Mind not on task
Walking into the line of fire
Losing balance, traction or grip

Complacency is a lack of vigilance due to familiarity with a task.
Complacency is one of the leading causes of safety related incidents occurring in the workplace. Once employees have been fulfilling their role for an extended period of time their confidence grows and their awareness decreases which results in lack of concentration and foresight. Employees can go into ‘autopilot’ and stop paying attention to what they are actually doing.
The same can occur when doing safety related tasks. Incident prevention, hazard awareness and general occupational health and safety have become an integral part of any workplace. Employees are needed to be provided with comprehensive training on health and safety in induction, ongoing training, reminders and daily hazard analyses. Occupational health and safety has become part of everyday life and a regular practice in most employees’ roles.
Although an increase in safety awareness is a positive and would likely have prevented many workplace incidents, the constant use of safety procedures can result in employees becoming complacent, lazy, overly comfortable or uninterested when following health and safety procedures. This can cause important steps to be skipped which may result in a preventable incident occurring. When it comes to safety, complacency can be a major risk.
One example of complacency in using safety procedures in the workplace is the use of job hazard analyses (JHAs) or job safety analyses (JSAs) before doing a task. If employees complete the same task often, instead of filling out a new JHA/JSA every time (as they should) and actively thinking about the risks involved in the task, the employees may copy/photocopy previous documents, fail to fill them out or skim over them briefly. This could cause hazards to be missed.
Another example of complacency is the persistent use of fluoro work wear in the workplace. Nowadays, any person not involved in an office role seems to wear some aspect of fluoro in their clothing attire to draw attention to the person. However, as fluoro is now so common, people have become ‘used to’ the colour and fail notice it as much. Fluoro is no longer a huge warning sign and people can simply glaze over its presence. This can result in employees not noticing other employees in their way, even while wearing fluoro safety gear and this may cause risks to employees.
Employers have a duty of ensuring their workplace is free from hazards. Some of the ways to combat employee complacency in the workplace and fulfil employer’s duties are as follows:
Highlight the risk of becoming complacent with employees and have discussions about times when employees have become complacent and how they could resolve the situation.
Change employee’s routines regularly so they never become too comfortable in their job that they become lax.
If employees have an overly repetitive role, think about having rotations through this role so the employee never spends too much time on the same task.
Encourage employees to constantly think about what they are doing while they are doing it.
Constantly remind employees about possible safety hazards and the consequences. If these hazards are on their mind it is more likely employees will think about them when performing a task.
If you see employees taking short cuts or risks, remind them that safety procedures are in place for a reason and must be strictly followed.
Create safety habits in the workplace like always wearing seat belts or checking for other employees in the vicinity before reversing.
Try to make safety fun and interesting to keep employees engaged.
Bring in people from out of the work area to look at it periodically and challenge the way things are done as they will often identify risks those exposed to the workplace each day are used to and challenge the way the risk is managed.
Most organizations have not realized that root-cause analysis is geared toward machines and circuits rather than human beings. Human behavior almost always is more complex than the model of contributory and root cause describes. When workers get tired or distracted and are injured, their condition tends to be described as complacent, and that condition tends to get listed as a contributory or root cause of the accident. Such simple, linear thinking usually is inaccurate and ineffective at preventing future accidents.
Root-cause methodology also is flawed. The idea that five is the magic number down a causal chain has been disproved again and again. That you have reached a root cause when you run out of data and cannot answer the next-level "why" question equally is erroneous. The more appropriate question to ask is,
"When workers become complacent, what precautions do they most often fail to take?" The answer to this question will reveal the habits that need more focus and to be reinforced in the safety culture.
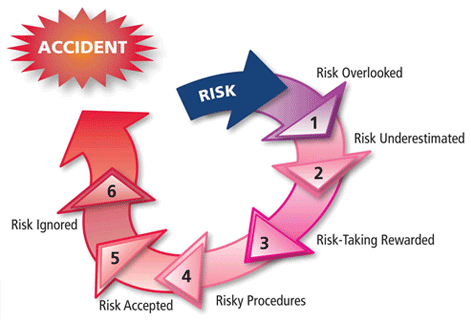
A behavioral Pareto analysis of accidents and near misses can be a real eye opener. The key to such an analysis is to determine not what caused the accident, but the behavior that could have prevented or lessened the severity of the accident. If the preventive behavior is complex and highly cognitive, then forming habits might not be the answer. However, if the preventive behavior is simple and rote, forming habits around these behaviors can be the solution.
Certain tasks require great planning and meticulous, conscious thought to carry out safely. Such tasks should not be addressed with cultural habit forming. However, in my experience, these complex tasks compose half or less of all risks attributed to complacency in most industries. In a few organizations, such tasks are negligible or non-existent.
In the end, safety solutions can be divided into conditional and behavioral. The behaviors can be divided into two categories as well: simple, repetitive behaviors and complex, cognitive behaviors. Root-cause analysis has great value in the conditional part of safety. Machines and circuits malfunction for a reason, which must be traced to its source to keep it from recurring. Human beings are more complex. When people "malfunction," we need to decide whether better habits or better thinking is needed. Forgetting that habits are part of the issue makes safety seem much more complicated than it has to be.
Root-cause analysis actually is a
contributing cause to the complacency dilemma
To learn how you can avoid these common workplace mindsets that cause many site accidents, reach out to our safety professionals. We’ll discuss your safety concerns to show you how to decrease injuries and keep profits up!
Comments