guidance and regulations that specify what stacking heights should be.
- Michael Roberts, CEO, Physec Compliance Group LLC
- Jun 1, 2016
- 8 min read
So I was at Menards today, picking up a grill.......naturally I was vigilant to everything around me. I asked an employee, "Is there any guidance or regulations that specify what stacking height should be for different materials in various forms of packaging merchandise.
The employee look very confused to my question. It befuddles me, that when running a business the size of a Menards, One would think that Safety is paramount and yet this employee had no clue as to what I was talking about......The sad part is that Menards will be the one who is held responsible. $$$$$$$$$$$$
GUIDELINE FOR STACKING HEIGHTS
There are a few guidelines that address safe stacking heights for different materials, such as:
1. OSHA’s standard 1917.14 states that: “Cargo, pallets and other material stored in tiers shall be stacked in such a manner as to provide stability against sliding and collapse.”
2. NFPA states that, due to fire concerns, empty pallet stacking be limited to 15 feet.
FACTORS THAT AFFECT STACKING HEIGHT
Having said that, and being a consultant, my answer to the question about safe stacking height has to be, “It depends.” To determine a safe height, you need to address these questions:
What are you stacking?
What kind of container is it in?
What is the gross weight of the package?
How many packages can be stacked on top of one another before the bottom fails?
What is the loading capacity of the floor? The deck? The shelving?
What are the temperature and humidity conditions for storage?
How will these conditions affect the packaging? The product?
You also need to consider safety and ergonomic issues:
How will the package be handled – by hand or with equipment?
Will the stack have to be broken down by hand?
If so, will the employee have to reach overhead? Repeatedly?
If a package falls from a height, how hazardous is it if it hits an employee on the head, the shoulder? With or without a hard hat?
Storage Handling
Stacking materials can be dangerous if workers do not follow safety guidelines. Falling materials and collapsing loads can crush or pin workers, causing injuries or death. To help prevent injuries when stacking materials, workers must do the following:
■ Stack lumber no more than 16 feet high if it is handled manually, and no more than 20 feet if using a forklift;
1926.250(b)(8)
Lumber:
1926.250(b)(8)(i)
Used lumber shall have all nails withdrawn before stacking.
..1926.250(b)(8)(ii)
1926.250(b)(8)(ii)
Lumber shall be stacked on level and solidly supported sills.
1926.250(b)(8)(iii)
Lumber shall be so stacked as to be stable and self-supporting.
1926.250(b)(8)(iv)
Lumber piles shall not exceed 20 feet in height provided that lumber to be handled manually shall not be stacked
more than 16 feet high.
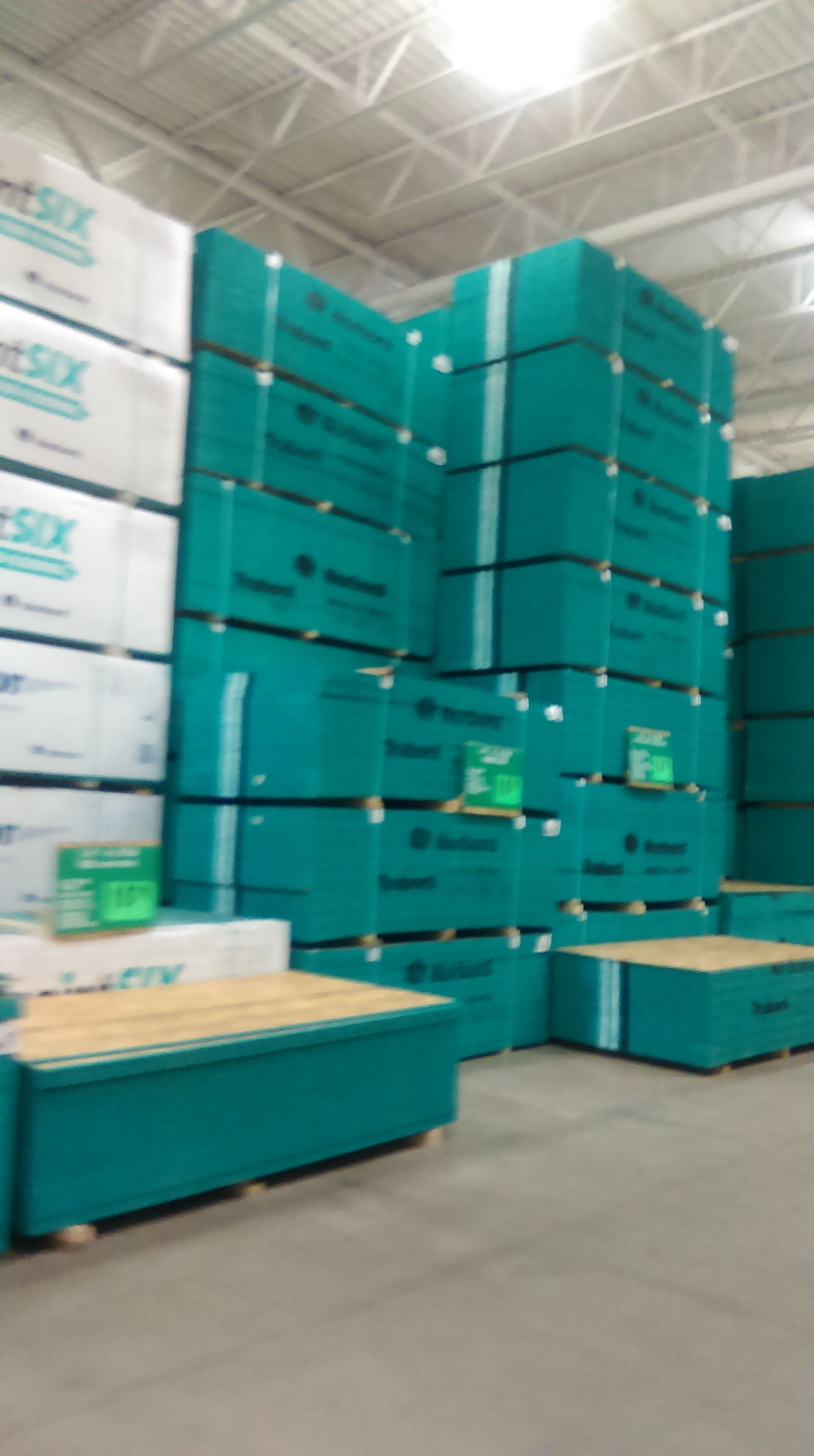
Pallet Racks
What follows are three racking issues that OSHA frequently cites under the General Duty Clause (these are based on actual OSHA citations issued to employers):
Rack columns not anchored to the floor. OSHA recommends that the bottom of all columns be of resisting the forces caused by the loads on the rack.
furnished with Steel column base plates, and be anchored to the floor with anchor bolts capable Load ratings not present on racking. OSHA recommends that load ratings be present that provide, at a minimum, the maximum permissible unit load and/or maximum uniformly distributed load per level, the average unit load, and maximum total load per bay. See ANSI/RMI MH16.1 for additional information.
Damaged racking. OSHA recommends that the employer develop a maintenance and inspection program for storage racks, which includes keeping aisles clear and providing sufficient clearance for material handling equipment, ensuring racks are properly aligned, plum, and level, per manufacturer’s instructions, as well as encouraging employees to promptly report any damage to racks.

Improper stacking and storage
Improper stacking and storage can result in injuries to workers and damage to costly materials. Make sure your material handlers stack up when it comes to safety.
Although OSHA does not provide much specific direction concerning safe stacking and storage, 29 CFR 1910.176(b) of the material handling standard does generally require secure workplace storage of materials. The regulation states: “Storage of material shall not create a hazard. Bags, containers, bundles, etc., stored in tiers shall be stacked, blocked, interlocked and limited in height so that they are stable and secure against sliding or collapse.”
General safe stacking and storage rules with which employees who handle materials should be familiar include:
Ensure that stacks are stable and self-supporting.
Observe height limitations when stacking materials.
Allow sufficient clearance around stacks for safe handling and easy access.
Make sure there is sufficient clearance between stacks and lights, heating pipes, and sprinkler heads.
Make sure stacks don’t block emergency exits, emergency equipment, or fire alarms.
In 1962, the first Wal-Mart and Kmart stores opened, and these merchants were about to "hit" the consumer in a big way. These stores operated on the formula that it was more efficient, less expensive, and more profitable to warehouse as much merchandise as possible on the sales floor, rather than in off-site warehouses or backroom storage areas. High stacking of merchandise was born, and a profitable business strategy at the expense of customer safety was created.
During the past decade, thousands of people have been injured, some killed, by falling merchandise while shopping in retail warehouses.
From doors, hot water heaters, and televisions to pet supplies, houseware goods, and toys, merchandise is falling off high shelves and causing injuries to customers at an alarming rate.
I t is in the nature of retail hardware and lumber operations to stock merchandise and stack it so it is easily accessible and readily available for sale. Each year, there are reported injuries to both customers and employees alike, due to falling merchandise. Typically, these preventable accidents happen when products are being stacked or unstacked. Storeowners must take all reasonable steps to ensure their operations are kept free from products, substances and equipment that pose an obvious threat of danger and injury. By providing an environment that is free from excessive liability is not only a smart business practice, but also contributes to a positive store morale.
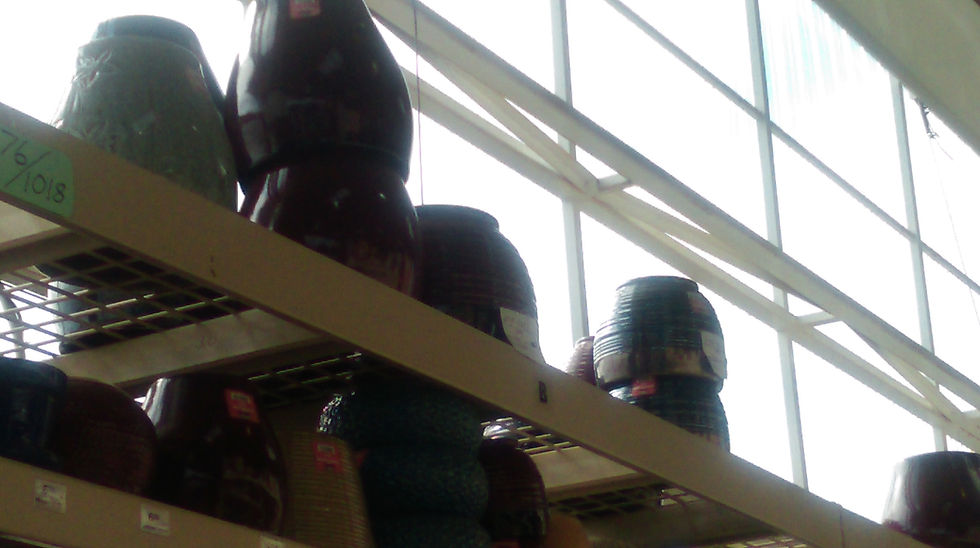

Since 1987, about 30,000 falling-merchandise incidents resulting in injuries to customers have occurred
During a recent 18-month period, 68 customers sued Home Depot for injuries sustained from falling merchandise.
Other companies operating a retail warehouse business include Lowe's, Kmart, Toys'R' Us, PetsMart, Costco, Sam's Club, and Staples. The retail warehouse business exploded during the 1990s and shows no signs of slowing down.
Falling-merchandise incidents have the following common characteristics.
High stacking. A trademark of the retail warehouse merchant is high stacking, characterized by safety experts as the storage of merchandise on the sales floor above eye level.
Merchandise is often stacked on shelves 15 feet above the sales floor. A sales clerk or customer must stretch, use a ladder or step stool, or climb on shelves to handle merchandise.
Unsecured merchandise. Typically, merchants do not use physical-restraining safety devices such as security bars, fencing, safety ties, and shelf extenders on high shelves because of the expense involved and the employee time it would take to use them. Kmart representatives have testified that use of the devices is simply "not practical."Wal-Mart takes the position that merchandise can be safely stacked on high shelves without the use of the devices.
Triggering events. Falling merchandise can be triggered by moving merchandise that has been stacked in an unstable manner; moving merchandise on one shelf in such a way that merchandise on an adjacent shelf falls, referred to as "push through"; stacking different size boxes on top of each other; and stacking heavy merchandise on top of lighter merchandise. Vibrations in and out of a store, merchandise left hanging over the lip of a shelf, and merchandise too large for a shelf can also cause the problem.
No warning of danger. Typically, the merchandise falls without any warning to unsuspecting customers. Notwithstanding that merchants know of the risk of falling merchandise from high stacking and the potential for serious injury to customers, they do not warn customers of these risks with signs, banners, or placards; do not cordon off shopping aisles when merchandise is being stocked or retrieved; and do not use spotters when stocking is in progress.
Customer not negligent. Generally, the customer is not the cause of the merchandise falling and is generally not charged with a duty to watch for falling merchandise or to expect merchandise to fall.
Improper training. Often store personnel are improperly trained, or not trained at all, in stocking techniques or in recognizing and correcting the hazards of falling merchandise. A number of incidents could be prevented if merchants would train employees in procedures for recognizing hazards and would ensure that the merchandise is safely stacked.
Nature of injuries. A significant percentage of injuries occur to the head, neck, back, and upper torso. Even light merchandise becomes dangerous when it falls from a high shelf. For example, a 5-pound object falling about 2 feet exerts a force of about 319 pounds.
Incidents tracked. Merchants in the retail warehouse business commonly track incidents. They know of the serious nature of the problem. Also, most know there are a far greater number of "near misses" than "hits."
Law of falling merchandise
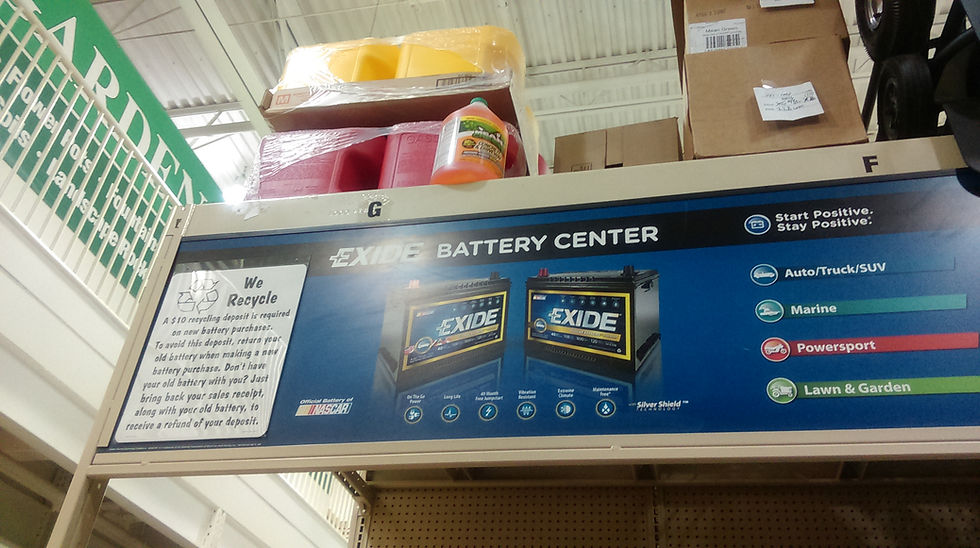
Falling merchandise is a relatively new and rapidly evolving area of premises liability. The seminal case that exposed the magnitude of the problem is Scharrel v. Wal-Mart Stores, Inc., in which it was discovered that between 1989 and 1994, 17,000 falling-merchandise incidents resulting in injuries to customers occurred in Wal-Mart stores.
A Denver jury awarded Phillip Scharrel more than $3 million for injuries he sustained when he was struck by 80 pounds of merchandise from a high shelf.
Since Scharrel, the problem has received national attention. Case law has developed favorably for customers. However, aggressive defense tactics often lead to lengthy, bitter, and expensive battles.
The law recognizes that merchants have a duty to invitees to exercise reasonable care to keep their premises in a reasonably safe condition and to warn of unsafe or hazardous conditions of which the merchant knows or should know through reasonable care and inspection.
It is well established that merchants owe a duty to their customers to keep their businesses, aisles, passages, and other public places in a reasonably safe condition and to use ordinary care to prevent injuries to customers.
A premises hazard is a condition posing an unreasonable risk of harm.
Merchants must take reasonable precautions to protect their customers from foreseeable dangers. An employee's knowledge of an unsafe condition may be imputed to the merchant.
Certain states have abolished the distinction between invitees and licensees, declaring that landowners owe the same duty of reasonable care to all people lawfully on their premises. Other states have codified common law premises liability.
Courts recognize that merchants must place merchandise on shelves safely so it will not fall.
The merchant must take affirmative steps to prevent it from falling, including checking the shelves periodically to ensure that merchandise is in a safe position and using devices to stabilize it.
The law recognizes that stacking merchandise on high shelves creates an unwarranted risk, and it is reasonably foreseeable that doing this contributes to the risk of merchandise falling.
Several courts have held that stacking boxed merchandise on a shelf above customers' heads creates an unreasonable danger.
Protection for the unwary shopper
Courts are increasingly protecting the unwary shopper from merchants who negligently stack merchandise too high. Merchants know that this practice presents an unwarranted and dangerous risk to the shopper. Store managers must anticipate that high-stacked unrestrained merchandise will fall, customers will move merchandise and cause it to be unstable or fall, and customers will try to reach for merchandise if help is not readily available. Courts are likely to admit evidence of other incidents in the same store or other stores in order to show that the merchant knew of the dangerous condition and also to negate the defense argument that the plaintiff's negligence is the only explanation for the fall. Finally, courts are increasingly refusing to instruct the jury on contributory or comparative negligence absent evidence of affirmative conduct on the part of the plaintiff. The defense argument that "accidents happen" does not fly in a falling-merchandise case.
Comments