Making the Business Case for Safety
- Michael Roberts, CEO, Physec Compliance Group LLC
- May 28, 2016
- 5 min read

As an employer (or person representing the employer), you have a duty to protect your workers from injury and illness on the job. Protecting workers also makes good business sense. Accidents and injuries are more expensive than many realize. Costs mount up quickly. But substantial savings in workers’ compensation and lost workdays are possible when injuries and illness decline. Physec Compliance Group LLC can help you.
Why Should I Care?
Let's start with a question – One of our clients had ten recordable injuries. Did they do a good job or a poor job?
Obviously, that question depends on three factors:
How many employees worked for the company;
How many hours were worked by those employees; and
What industry was the employer in
For instance, if our client employed five people who worked 40 hours per week, then ten injuries would be a very bad record. However if the client employed 1,000 people who worked an average of 40 hours per week, ten injuries would not be so bad.
Furthermore, the ten injuries may be considered high in a low hazard industry such as a call center. Those same ten injuries may be considered very low in a high hazard industry such as construction.
Why is this important?
Because your record is dependant on these factors and each company employees a different number of employees, we rarely speak in terms of how many injuries we had. In fact OSHA doesn't typically ask "How many injuries did you have"? Instead, they ask "What is your Injury & Illness Incident Rate" or "What is your DART rate"?
What are Incidence Rates?
The incidence rate is a trending number based on your Injury & Illness rates if you had worked 200,000 hours. Why does OSHA use the 200,000 hour benchmark? Quite simply, 200,000 hours are the hours worked by 100 employees, averaging 40 hours per week over a 50 week span (two weeks taken away for holidays).
If the total hours your employees worked is less than 200,000 or more than 200,000 it doesn't matter, we use this number to establish a trending benchmark.
What is a DART Rate?
The DART rate stands for "Days Away, Restrictions and Transfers". This number is also based on trending over 200,000 hours but its not based on total injuries. Its based only on those injuries and illnesses severe enough to warrant "Days Away, Restrictions and Transfers".
As a general rule of thumb, you want to have a lower DART rate than Incidence rate.
How can I figure my Incidence and DART Rates?
We have developed an "Incidence Rate Calculator" that easily figures both your Incidence rate and your DART rate (see example below).
Why is safety and health important for me?
Compliance with OSHA regulations is essential. Compliance along with an effective voluntary safety and health program can help reduce your costs and injuries and illnesses. An organized, carefully crafted plan that systematically focuses on workplace hazards and employee training is critical.
How can I reduce employee injuries and illnesses?
Buy-in from every manager and employee is essential. Everyone has to work at safety and health.
Each safety and health program should be tailored to fit your company,
to blend with its unique operations and culture, and
to help employers maintain a system that continually addresses workplace hazards.
How do I develop this program?
There are four elements that every effective program should have:
· management leadership and employee involvement,
· workplace analysis,
· hazard prevention and control, and
· safety and health training and education.
What do you mean by management commitment and employee involvement?
Employers and employees work together to make safety and health a priority.
For example, this partnership can be achieved when you:
· Post the company’s written safety and health policy for all to see
· Involve employees in policymaking on safety and health issues
· Take an active part in safety activities
· Hold meetings that focus on employee safety and health
· Abide by all safety and health rules
· Show your commitment by investing time, effort, and money in your safety and health program.

What’s a worksite analysis and how often do I have to do it?
A worksite analysis means that you and your employees analyze all worksite conditions to identify and eliminate existing or potential hazards. This should be done on a regular and timely basis. There should be a current hazard analysis for all jobs and processes that all employees know and understand.
To do this, you could:
· Become aware of hazards in your industry
· Create safety teams
· Encourage employees to report workplace hazards
· Examine history of worksite conditions
· Have an adequate system for reporting hazards
· Have trained personnel conduct inspections of the worksite and correct hazards
· Ensure that any changes in process or new high-hazard facilities are reviewed by a competent person
· Seek assistance from safety and health experts.
What else do I need to know?
The next part of a good safety and health program means that you continually review your work environment and work practices to control or prevent workplace hazards. This can be done when you:
· Regularly and thoroughly maintain equipment
· Ensure that hazard correction procedures are in place
· Ensure that employees know how to use and maintain personal protective equipment
· Ensure that all employees understand and follow safe work procedures
· Make sure that, where necessary, you have a medical program tailored to your facility to help prevent workplace hazards and exposures.
It is important that everyone in the workplace be properly trained, from the floor worker to the supervisors, managers, contractors, and part-time and temporary employees. This can be done when you:
· Allow only properly authorized and instructed employees to do any job
· Make sure no employees do any job that appears unsafe
· Hold emergency preparedness drills for employees
· Pay particular attention to employees learning new operations to make sure they have the proper job skills and awareness of hazards
· Train supervisors and managers to recognize hazards and understand their responsibilities.
Case Studies: Good Examples of Cost Reduction Through Proactive Safety Programs
* Liberty Mutual Insurance Company released a report titled: A Majority of U.S. Businesses Report Workplace Safety Delivers a Return on Investment. The Liberty Mutual survey shows 61 percent of executives say $3 or more is saved for each $1 invested in workplace safety.
* A coal mining company in Charleston West Virginia has attained a competitive advantage through investment in SH&E programs. The company claims its worker compensation rate is $1.28 per $100 in payroll as opposed to its competitor's rate of $13.78.
* Fall protection program implementation reduced one employer's accident costs by 96 percent - from $4.25 to $ 0.18 per person-hour
* Implementation of an consultation program reduced losses at a forklift manufacturing operation from $70,000 to $7,000 per year
* Implementation of an improved safety and health program reduced Servicemaster's worker's compensation costs by $2.4 million over a two-year period
OSHA's Office of Regulatory Analysis has stated: …that our evidence suggests that companies that implement effective safety and health cans expect reductions of 20% or greater in their injury and illness rates and a return of $4 to $6 for every $1 invested...
Would you like to realize similar savings? To achieve these types of savings you must develop the following six critical components of a successful health & safety program:
1. Employee Training
2. Written Health & Safety Programs
3. Injury & Illness Recordkeeping
4. Understanding of the OSHA regulations
5. Proactive site inspection
6. Displaying the OSHA poster
If you can complete these six components, you’ll be well on to way to compliance and a healthy & safe workplace!
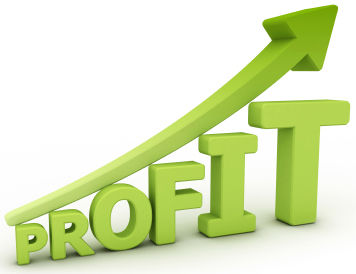
Physec Compliance Group LLC's mission is to promote and ensure workplace safety and health and reduce workplace fatalities, injuries and illnesses. Although we are constantly facing new challenges from new industries, new technologies, and an ever-changing workforce, Physec Compliance Group LLC's mission remains the same.
Establishing & Reaching Safety Related Goals.
Comments