Safety: For a Change
- Michael Roberts, CEO, Physec Compliance Group LLC
- May 22, 2016
- 10 min read
Safety: For a Change
Safety isn’t a matter of luck. It has to be taken seriously. We are all too valuable to ourselves, our families, and our friends to trust our lives and limbs to plain dumb chance. In 2016, Physec Compliance Group will promote “Safety. For a change.”
—a concerted effort and campaign to improve awareness of Wisconsin's workplace safety record and to encourage safer workplaces and behaviors. The effort will include a comprehensive study into cost factors, extensive research into attitudes, educational conferences and a statewide awareness campaigns.
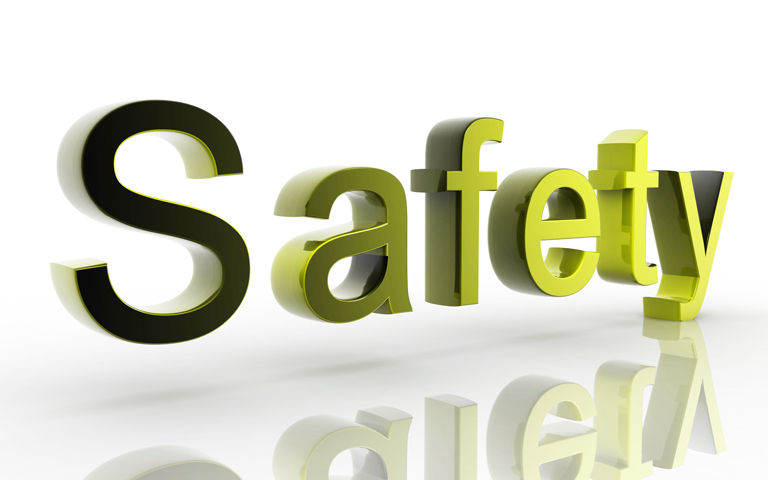
The Importance of Safety
A serious workplace injury or death changes lives forever – for families, friends, communities, and coworkers too. Human loss and suffering is immeasurable.
Occupational injuries and illnesses can provoke major crises for the families in which they occur. In addition to major financial burdens, they can impose substantial time demands on uninjured family members. Today, when many families are operating with very little free time, family resources may be stretched to the breaking point.
Every person who leaves for work in the morning should expect to return home at night in good health. Can you imagine the knock on the door to tell you your loved one will never be returning home? Or the phone call to say he’s in the hospital and may never walk again? Ensuring that husbands return to their wives, wives to their husbands, parents to their children, and friends to their friends — that is the most important reason to create a safe and healthy work environment.
But it isn’t the only reason.
REDUCING INJURIES REDUCES COSTS TO YOUR BUSINESS:
If a worker is injured on the job, it costs the company:
- in lost work hours,
- increased insurance rates,
- workers’ compensation premiums and
- possible litigation.
Productivity is lost when other workers have to stop work to deal with the injury. Even after the injured employee has been sent home or taken to the hospital, other employees may be distracted or need to take time off from work in the aftermath of the incident. Even a single injury can have far-reaching and debilitating effects on your business.
SAFE WORKERS ARE LOYAL WORKERS:
Any business knows that employee attrition and absenteeism can be major obstacles.
When you create a healthy and safe workplace, you reduce those issues in several ways. By budgeting for safety improvements and making safety part of your operational plan, you engender trust. By involving employees in safety decisions—through reporting, committees, walk-throughs and meetings—you show that their opinion matters to you. By following through on their input and improving safety, you prove quite tangibly that you care about their well-being. Workers typically respond by working harder, showing more pride in their jobs and remaining loyal.
SAFETY IMPROVES QUALITY:
Time and again, companies that put safety first turn out higher quality products. In some cases, that’s because a safe workplace tends to be a more efficient one, free of debris and tangles of cords. In other cases, it’s a matter of focus. By working in a clean, efficient environment, workers are able to reduce distractions and truly focus on the quality of what they do. The results? Better products that create customer loyalty, bigger margins and increased sales.
In these ways and others workplace safety is about much more than legislation. It’s about creating the kind of productive, efficient, happy and inspiring workplace we all want to be part of. It’s about creating a highly profitable company. And that’s why it’s important.
Employer Role:
Safety from the Top
Collectively, businesses could save $145 million per year by getting work injury rates in line with national averages. That number, found during an in-depth study conducted by Physec Compliance Group only accounts for direct costs, such as insurance premiums and related health care. If lost productivity and retraining were included, the dollar figure would easily be double that.
As a business you pay higher workers’ comp premiums than you would in any other state in our region. Injured employees at workplaces stay out of work and on workers’ comp as much as 26 percent longer than those in other states. But the number one reason for the high costs is simple: workers get hurt more often—job for job, age for age—than all but one other state in the country.
The good news? This is a problem we can solve through education and program adoption. As an employer, your role is pretty straightforward:
Provide a safe, healthful work environment for your employees.
Show you place a high value on safety by creating a culture of safety in your company.
Encourage shared responsibility for safety among your employees.
As an employer, you want to make sure you have a safe workplace. However, this is sometimes easier said than done. Most of us lack the required experience and expertise to know all the dangers our employees can face, and as such, fall short in the safety department.
Over the years, OSHA has dealt with many safety issues that have paved the way for new rules and regulations for employers to follow. Even if you do not like government overreach into your business, OSHA regulations are something you need to be aware of. They provide us with the oversight necessary to ensure the safest workplace possible.
Reasons Why Employers Need to Take Note
I’ve already stated the obvious, but will reiterate it here. I don’t think there is anyone running a business who doesn’t care about the safety of their employees—it would be inhumane not to. Also, most of us work within our own business so ensuring a safe workplace benefits us all.
Another reason to take note is lack of experience. There are many workplace hazards that you may not be aware of. Unless you work for OSHA, it is unlikely that you will know about every safety hazard to look for and to protect your employees from. It is important to take note of OSHA regulations in order to educate yourself on safety in the workplace.
Finally, it’s the law. Even if you are that rare person who really doesn’t care about employee safety, you need to be aware that failing to protect your employees can wind up costing you civilly as well as criminally—yes, criminally.
Legal Ramifications for Non-Compliance With OSHA
Okay, let’s talk a minute about penalties. We already know that dangers in the workplace can cause harm (including loss of life) for employees. However, let’s take a look at what can happen when employers fail to follow OSHA regulations.
OSHA fines are fairly easy to understand. In fact, they are some of the lowest levied by any federal agency. However, the “lowest” is still a significant amount that can be avoided if the standards are followed.
Each violation can carry a fine of up to $7,000. Repeat violator? Then the maximum can be up to $70,000. These figures are currently being evaluated and could increase to $12,600 and $126,000 respectively. Employers should not be as worried about paying out money as they should be in potential loss of freedom.
OSHA has referred more than 150 cases to the Justice Department for criminal prosecution. The result of these prosecutions has not only included fines and costs, but also prison time for those who willfully violated OSHA regulations. It will also be getting tougher for employers whose willful conduct results in the death of an employee.
In December 2015, OSHA entered into a memorandum of understanding with the Justice Department relating to criminal enforcement. In accordance with the MOU, employers whose willful conduct results in death can face penalties of up to 25 years in prison as opposed to the “standard” 6 months.
Now let’s look outside of the penalties that can be levied by OSHA and the U.S. DOJ. As with just about all government enforcement from the Department of Labor, a violation can be used as proof that a company is civilly liable. For example, if OSHA finds a company failed to implement safety standards, and the result was an employee getting hurt, this can be used as proof of liability in a civil suit brought against the employer.
What Should You Be Doing?
The first thing you need to do as an employer is be aware of your responsibilities. The OSHA website contains quite a bit of information for you, including the entire list of guidelines you must follow. These guidelines are extensive and time consuming to read, which is why workplace posters are also available.
Workplace posters and signage are important. They make things easy to understand and provide valuable information for both employers and their employees. If you are unsure of what posters you should have, contact OSHA as they have a list of those that are required—yes, required. It is a violation to NOT display certain posters. Which reminds me, make sure to keep the posters up-to-date.
Training is also extremely important. You can have all the posters in the world and some people will still not read them. So, training is something you need to implement. Keep in mind that many people are visual learners. As such, make sure to integrate safety labels and signs into your training program. People are more likely to remember dangers from visualizations than they are from reading endless words on posters.
Record-keeping should be a top priority, not only to ensure you are providing the safest possible workplace, but also to protect you against litigation. OSHA has specific record-keeping requirements, but it is recommended that you go above and beyond providing a safe workplace in case you ever fall victim of a civil suit.
Finally, stay up-to-date on everything OSHA. You may think you are in the best position now, but rules change frequently. Make sure to implement a training system so that you become aware of current laws regarding workplace safety. It could be the difference between having a safe work environment and spending time in prison.
So What Should You Be Doing....
Creating the Right Safety Culture for Your Workplace
How to Build Your Safety Program
A structured, deliberate approach to safety is the best way to optimize effectiveness and ensure you reap the full reward of your program.
1. Commit to workplace safety.
The first step in building a safety program is getting a commitment from the company’s executives to safety and wellness. This commitment should rank high on every executive’s priority list. One way of achieving this is to include the importance of workplace safety in the company’s mission statement. Management can also demonstrate this by investigating all workplace accidents and encouraging employees to follow all safety procedures.
2. Identify hazards and assess risks.
A hazard is a situation or event with the potential to cause harm. The risk is the likelihood that someone could be harmed by that hazard together with an indication of how serious the harm could be. The law doesn’t require you to eliminate all risk, but you are required to protect people as far as is reasonably practical. Talking with employees is one way of identifying hazards. They may have noticed things that are not immediately obvious to you. Inspecting the workplace is another. A comprehensive workplace survey will help identify safety hazards.
You should distinguish between:
Workplace hazards, such as a workshop’s layout.
Activity hazards, such as using grinding machinery in your workshop.
Environmental hazards, such as the dust created when using grinding machinery.
3. Develop written programs and processes.
Management should be accountable for clearly stipulating safety requirements for employees to follow. To create a safety culture that exhibits accountability, employee job descriptions must be clear and in writing, and must state specifically the issues and requirements regarding safety and health responsibilities. Having these requirements in writing is critical because it greatly reduces opportunities for ambivalence and misinterpretation.
Not all safety regulations require written plans, but there are several that do. Below is a list of common regulations that require a written plan or program.
Hazard Communication Program.
Lockout / Tagout Program (energy control procedures).
Respiratory Protection Program.
Personal Protective Equipment (hazard assessment).
Bloodborne Pathogens Post-exposure Plan.
Emergency Actions Plans.
Permit-required Confined Spaces.
Electrical Safety.
Fire Prevention Plan.
Hearing Conservation Program.
Trenching and Excavation Safety.
4. Educate employees.
Training is an indispensable part of every employer’s safety and health program for protecting employees from injuries and illnesses. Research shows that those who are new on the job have a higher rate of accidents and injuries than more experienced workers. If lack of knowledge of specific job hazards and of proper work practices is even partly to blame for this higher injury rate, then training will help provide a solution.
Many OSHA standards specifically require the employer to train employees in the safety and health aspects of their jobs. Other OSHA standards make it the employer’s responsibility to limit certain job assignments to employees who are “certified,” “competent” or “qualified”—meaning that they have had special previous training, in or out of the workplace.
OSHA has developed voluntary training guidelines to assist employers in providing the safety and health information and instruction needed for their employees to work at minimal risk to themselves, to fellow employees and to the public.
Good Rules of Thumb—provide training when you:
First hire employees (include both general and job specific).
Transfer employee between departments, or assign new responsibilities.
Change or implement new processes, substances and/or equipment.
Uncover special hazards (i.e., excavations, confined spaces, respiratory, etc.) or hazards that were previously not noticed.
Believe refresher training is needed or required by regulation.
5. Investigate/report all accidents and incidents.
All incidents should be reported and investigated regardless of the severity of the outcome. The outcome is generally not controllable, but the incident itself is more often than not an event that is preventable. The purpose of an investigation is to:
Determine the causes of the incident. Take care to remind the injured employee(s) and witness(s) that you are not attempting to place blame; you are on a fact-finding mission.
Identify what can be done to reduce the chances of a similar accident happening again.
Take corrective action and monitor results.
6. Evaluate safety processes each year.
Determine the strengths and weaknesses within your safety processes. Look for ways to improve them and ultimately reduce workplace accidents and injuries. Implement new and modify existing processes as needed.
DEVELOP A WRITTEN PLAN
The greatest factor by far in Wisconsin's high workplace injury costs is our work injury rate. Across our state, we injure more people in a wider variety of occupations than do other states. The only solution to this problem is to instill a culture of safety in every workplace. That begins with a tailored safety program. The most successful programs have the following.
Structured Safety Orientation
—The safest workplaces stress the importance of safety beginning with an employee’s first day. Orientations include informing employees of their rights, walking them through your safety program and talking about what to do in the event of an injury.
Open Communication
— Create a culture where employees are encouraged to raise questions about safety and pursue safer ways of accomplishing their work. Clearly spell out all safety procedures, as well as procedures for incident reporting and Stay at Work/Return to Work programs.
A Management that Values Safety
— If you clearly value safety, your employees will too. Create an employee-led safety committee, include safety topics in management meetings, reward employees for safety, hold employees who work unsafely accountable and make safety part of performance reviews. If something is unsafe, change it. Savings down the road will outweigh the cost.
Comments