Understanding the Value of Safety, the return on value for safety and the economic costs of just on
- Michael Roberts, CEO, Physec Compliance Group LLC
- May 19, 2016
- 4 min read
Understanding the Value of Safety,
the return on value for safety and
the economic costs of just one (1) company's inaction
These companies that have achieved safety excellence in 2015
Apollo Mechanical,
BMWC Constructors Inc.,
CJ Drilling Inc.,
Commonwealth Edison,
Dow Corning Corp.,
FHG Inc.,
Fisher Contracting Co.,
Merjent Inc.,
Parker Drilling,
PATS Aircraft Systems,
Rummel Construction Inc.,
Solenis,
Smiths Medical,
Solid Platforms Inc.,
USG Corp. and
Victaulic Co.
These companies represent as few as 100 employees and as many as 50,000, have one location or dozens of locations, have one safety representative or large EHS staffs. What they have in common is they recognize the return on value for safety.
“Return on the value of safety is a metric that applies to every business, though it carries particular significance in manufacturing, oil and gas, transportation, chemical, construction and recycling,
“It is 2016 and some companies still believe that on-the-job injuries and illnesses are a cost of doing business.”
Costs
In addition to their social costs, workplace injuries and illnesses have a major impact on an employer's bottom line. It has been estimated that employers pay almost $1 billion per week for direct workers' compensation costs alone. The costs of workplace injuries and illnesses include direct and indirect costs. Direct costs include workers' compensation payments, medical expenses, and costs for legal services.
Examples of indirect costs include training replacement employees, accident investigation and implementation of corrective measures, lost productivity, repairs of damaged equipment and property, and costs associated with lower employee morale and absenteeism.
The following resource provides background on the costs of workplace injuries and illnesses and how Occupational injuries and fatalities in one industry, cost Maryland residents $712.8 million between 2008 and 2010. The cause? - INACTION
Economic burden of workplace injuries and fatalities in Maryland's General industry by estimating the direct, indirect, and quality of life costs resulting from fatal and nonfatal injuries. The report estimates that fatalities and injuries cost the Maryland economy $712.8 million in just 2 years ( from 2008 to 2010.)
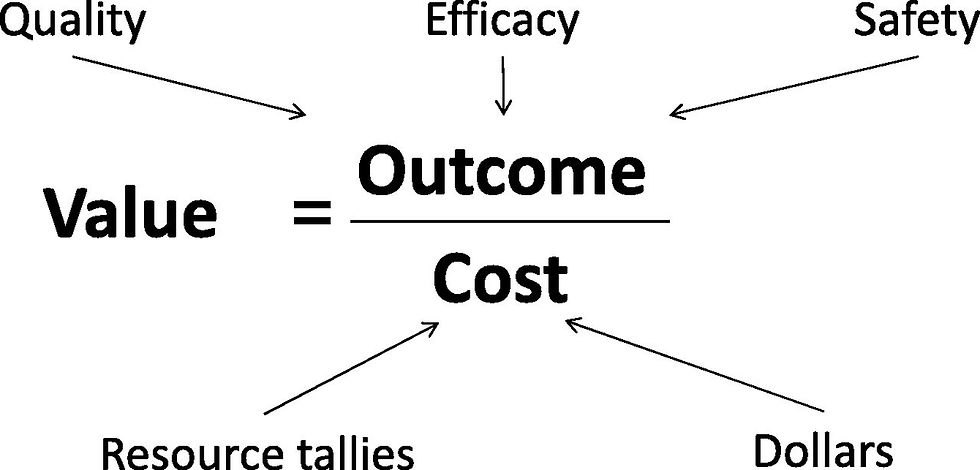
To achieve safety excellence,
a company has to adopt a multi-faceted approach in safety. "If you think of a safety program as a wheel and these elements as spokes, removing one of the spokes would compromise the integrity of the wheel. And on that same line it takes Management commitment – "If company leadership does not endorse, support and live a safety culture, we would see no success,"
Some of the common denominators have become apparent. To name just a few:
Upper management commitment
Comprehensive training
Employee involvement
Safety playing an integral role in daily operations
Safety training – In addition to the orientation, task-specific safety training occurs throughout an employee's career
Safety auditing – "By auditing our work areas on a continual basis, we can identify hazardous acts and conditions and correct them before they become an incident or loss,"
Incident reporting/lessons learned – The company identifies all incidents to determine root cause and identify any gaps within the safety program. Investigation follow up for Improved Performance report.
Safety discipline – "Discipline is not a popular element of our safety program, However, it is essential to the success of the business. Safety discipline allows us to intervene when unsafe actions have the potential to result in injury or incident of loss. Our safety program does not provide a 'three-strike' opportunity, rather discipline is based on the severity of the violation."
Although Physec Compliance Group is willing to place safety above the bottom line, the fact is that safety and profitability are not the polar opposites that some companies perceive them to be. Physec Compliance Group sees things quite differently, as we understand that work-related injuries and fatalities are a cost – in human and financial terms – that no company should expect to incur!
Physec Compliance Group knows and understands the importance of safety committees, training, job-hazard analyses, audits, stop-work authority, employee involvement and management visibility. We get the symbiotic relationship between safety and productivity, profits, morale and employee retention.
Safety Philosophy
At the core of Physec Compliance Group safety philosophy it is the belief that employees are most productive when they are involved in the safety process.
“Workers are the most important experts in identifying hazards, We rely heavily on workers identifying hazards and proposing how those hazards can be mitigated.”
Physec Compliance Group also institutes a stop-work authority, which not only empowers employees to cease operations if a hazardous condition presents itself, but obligates them to do so. For such a system to work, employees must be confident they can safely stop work without facing adverse consequences. That’s a priority,”
To ensure workers feel comfortable addressing safety concerns, Physec Compliance Group acts as a third-party consultant to conduct employee surveys to assess workers’ impressions of the safety culture. Survey results usually find that 99 percent of employees would take action if they observe unsafe conditions. When employees do have concerns, Physec Compliance Group is quick to act.
Physec Compliance Group is Committed to conducting business in a manner that protects the public, you and your customers, your employees, and the environment.
Physec Compliance Group Services will:
Communicate to each customer, supervisor, employee, and sub-contractor his/her safety responsibilities and regularly measure safety performance.
Adhere fully with all applicable OSHA and environmental laws/regulations.
Operate our business using the sound safety practices necessary to protect personnel, property and the environment.
Conduct JSA (Job Safety Analysis) assessments before starting a new activity, make all personnel aware of potential hazards, and provide controls to minimize or eliminiate risks.
Ensure training is provided to protect your employees, the environment, your property and the public.
Retain professional staff to support Environmental, Health and Safety activities.
Evaluate and report safety performance for continuous improvement
Nothing Left to Chance
Since Physec Compliance Group took over a retail safety compliance contract 3 years ago, it has cut reportable events by 50 percent, has had no reportable lockout/tagout events in the last 2 years and has reduced overall loss from 2.38% down to .19% within the first year increasing their ROI.. The Physec Compliance Group maintains a total recordable case rate of less than one case per 200,000 hours worked.
The Physec Compliance Group comprehensive approach to workplace safety includes a safety council and a host of programs that address issues including ergonomics, wellness, mentoring, safety auditing, electrical hazards, heat stress, chemical vapors, traffic and even insect bites. Clearly, the company isn’t willing to chance its workers’ well-being.

Comments